AI Manufacturing Companies Supporting Industry 4.0 in Thailand
AI manufacturing companies are at the forefront of this transformation. These companies provide the tools and expertise to automate production lines, optimise supply chains, reduce energy consumption, and increase operational intelligence. Thai manufacturers are increasingly partnering with AI experts to transition from legacy operations to predictive, adaptive, and intelligent systems. In this blog, we explore the leading companies driving AI-powered innovation in Thai manufacturing, starting with SmartOSC.
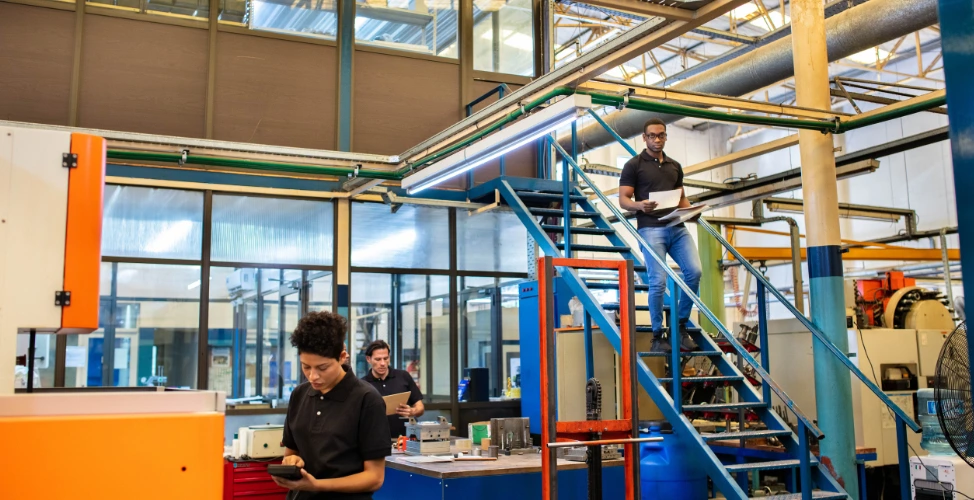
Why AI Is Essential to Thailand’s Manufacturing Future
Thailand is rapidly positioning itself as a smart manufacturing hub in Southeast Asia, with Industry 4.0 at the heart of its national development strategy. Initiatives like Thailand 4.0 and the Eastern Economic Corridor (EEC) are accelerating the adoption of advanced technologies, including artificial intelligence (AI), across the industrial sector. In this landscape, AI manufacturing companies are playing a critical role by helping factories become more agile, efficient, and data-driven. As the region navigates labour shortages, global competition, and economic transformation, AI-driven innovation is proving essential for building resilient and future-ready manufacturing ecosystems.
The Rise of Industry 4.0 in Thailand
Industry 4.0 refers to the convergence of smart technologies, such as AI, IoT, robotics, and cloud computing, within industrial operations. Thailand’s roadmap toward smart industry includes upgrading physical and digital infrastructure, promoting R&D, and attracting high-tech investment into strategic sectors like automotive, electronics, and food processing.
According to Thailand’s Ministry of Industry, over 40% of large Thai manufacturers have begun adopting at least one Industry 4.0 technology, a figure projected to rise sharply by 2026. At the core of this transformation, AI manufacturing companies are driving innovation by enabling automation, advanced analytics, and seamless system integration across production environments. Their expertise is helping Thai manufacturers enhance efficiency, reduce costs, and stay competitive in an increasingly digital industrial landscape.
Challenges Thai Manufacturers Face Without AI
Despite progress, many manufacturers still rely on outdated systems, manual inspections, and siloed data environments. This results in:
- Unplanned downtime and reactive maintenance
- Inefficient quality assurance and error detection
- Inventory mismanagement and overproduction
- Labour-intensive processes that can’t scale
- Inconsistent safety and compliance tracking
Without AI, manufacturers struggle to respond quickly to market changes, rising material costs, and global supply chain disruptions.
See more: Enterprise Services from Artificial General Intelligence Companies in Thailand
Top AI Manufacturing Companies Driving Innovation in Thailand
SmartOSC
SmartOSC is a leading digital transformation consultancy in the Asia-Pacific region and is increasingly recognised among top AI manufacturing companies driving innovation in Thailand. With over 18 years of industry experience, SmartOSC has earned a strong reputation for delivering scalable, secure, and AI-powered solutions that address the unique challenges faced by Thai manufacturers. Their tailored approach helps businesses modernise operations, boost productivity, and stay competitive in the evolving Industry 4.0 landscape.
As the manufacturing sector becomes increasingly reliant on data-driven processes, SmartOSC provides an end-to-end approach to AI integration, from assessment and solution design to deployment, optimisation, and workforce enablement. Their strategy-first methodology ensures that AI is not applied as a one-size-fits-all tool but as a business-aligned solution that enhances both efficiency and agility on the factory floor.
SmartOSC’s core AI capabilities in manufacturing include:
- AI-powered predictive maintenance: Leveraging sensor data and historical equipment logs to predict failures before they occur, enabling Thai manufacturers to reduce unplanned downtime and extend the lifespan of critical assets.
- Visual inspection systems: Using computer vision, machine learning, and edge AI to conduct real-time defect detection, dimensional checks, and process monitoring on high-speed production lines.
- Smart inventory and demand forecasting: Building models that assess sales trends, supply chain constraints, and customer behaviour to automate restocking and reduce overproduction.
- Cloud-based industrial data platforms: Integrating machine data, ERP records, and production KPIs into centralised dashboards, delivering real-time insights to managers, engineers, and executives.
- Factory system integration: Seamlessly connecting AI models with programmable logic controllers (PLCs), manufacturing execution systems (MES), and IoT devices for closed-loop automation.
SmartOSC’s client portfolio in Thailand covers key industries such as automotive, logistics, electronics, and industrial equipment. In every engagement, the team blends sector-specific expertise, local regulatory knowledge, and global best practices to deliver measurable outcomes. Their ability to embed AI and Data Analytics into these tailored solutions empowers Thai enterprises to optimize operations, gain predictive insights, and drive sustained business value.
Beyond implementation, SmartOSC also helps manufacturers build internal AI readiness through workforce training, digital governance planning, and analytics centre-of-excellence (CoE) development. Their role as a strategic partner ensures manufacturers can continuously evolve their digital capabilities and remain competitive in the Industry 4.0 era.
Siemens Thailand
Siemens is globally recognised as one of the leading AI manufacturing companies, with its Thailand division playing a key role in advancing smart factory technologies. Through its MindSphere platform, Siemens supports the integration of AI applications such as machine learning, digital twins, and predictive diagnostics. These solutions are particularly impactful in energy-intensive and precision-driven manufacturing environments, helping Thai industries optimise efficiency, reduce downtime, and accelerate their Industry 4.0 transformation.
Hitachi Asia
Hitachi’s AI-driven Lumada platform is widely used in Thailand’s infrastructure and industrial sectors. Their focus includes smart energy management, factory automation, and maintenance optimization. Hitachi combines operational technology (OT) with IT for holistic transformation.
ABB Thailand
ABB brings robotics, automation, and AI under one roof. Its Thailand operations help manufacturers deploy collaborative robots (cobots), AI-assisted control systems, and predictive maintenance tools. ABB also supports electrification and sustainability goals.
IBM Thailand
IBM is recognized as one of the prominent AI manufacturing companies, offering advanced industrial AI solutions through its Watson platform and hybrid cloud architecture. In Thailand, IBM collaborates with manufacturers to implement AI-driven capabilities such as supply chain planning, anomaly detection, and intelligent automation. Alongside these innovations, IBM also provides robust cybersecurity and data governance services, ensuring that Thai manufacturers can adopt AI with both confidence and compliance.
Schneider Electric
Schneider Electric is a pioneer in energy-efficient smart manufacturing. Their AI-driven EcoStruxure platform is used for predictive asset management, process optimisation, and intelligent energy monitoring in Thai factories.
Mitsubishi Electric Thailand
Mitsubishi Electric provides AI-based factory automation systems such as MELFA robots and e-F@ctory. Their systems are known for reliability in discrete manufacturing and electronics assembly lines.
Bosch Thailand
Bosch’s Industrial IoT and AI solutions enable smart production and supply chain transparency. Their applications in Thailand focus on quality control, maintenance analytics, and connected industrial environments.
Honeywell Thailand
Honeywell offers industrial AI for process industries including chemicals and food processing. Their Forge platform supports real-time performance monitoring, prescriptive analytics, and remote diagnostics for Thai manufacturers.
Cognex
Cognex is a key player among AI manufacturing IT services, specialising in machine vision and AI-powered visual inspection systems. In Thailand, Cognex supports manufacturers in industries such as packaging, automotive, and electronics, where high-speed, high-precision defect detection is essential. Their solutions help enhance quality control, reduce waste, and improve overall production efficiency in advanced manufacturing environments.
Key Use Cases for AI in Thai Manufacturing
Predictive Maintenance
AI algorithms analyse historical sensor and machine data to identify wear patterns and failure risks. This enables Thai manufacturers to schedule maintenance proactively, reducing downtime, extending equipment life, and avoiding costly breakdowns.
Automated Quality Control & Visual Inspection
AI manufacturing companies are transforming quality control with AI-powered image recognition systems that detect defects in real time. These advanced solutions significantly improve inspection accuracy while minimizing human error and reducing delays across high-volume production lines, making them essential for manufacturers aiming to boost efficiency and maintain consistent product quality.
Demand Forecasting & Smart Inventory
Machine learning models improve forecasting accuracy by analysing market trends, customer demand, and supply variability. AI-driven inventory optimisation reduces stockouts and excess inventory, improving cash flow.
Workforce and Safety Optimisation
AI supports ergonomic planning, worker monitoring, and environment sensing to improve occupational safety. Wearable devices and computer vision can alert teams to hazards or non-compliance in real time.
Choosing the Right AI Partner for Your Factory in Thailand
Choosing the right partner from among the many AI manufacturing companies is essential for Thai businesses aiming to unlock the full potential of smart manufacturing. With a broad range of technologies, tools, and implementation approaches available, it’s crucial to select a company that aligns with specific operational requirements, industry standards, and the organisation’s level of digital maturity. The right AI partner can drive meaningful transformation by delivering tailored, scalable solutions that support long-term growth.
Here are the key factors Thai manufacturers should consider:
- Industry experience: Has the provider worked with your sector’s specific needs?
- Local presence and support: Do they understand Thai compliance, language, and workflows?
- Platform interoperability: Can their solution integrate with existing PLCs, ERP, and MES?
- Customisability and scalability: Will the system evolve with your production goals?
- Security and governance: Are data privacy and intellectual property safeguarded?
A good AI partner offers more than just tools, they help you plan, implement, train your team, and scale successfully.
Watch more: Scalable Data Analytics Consulting Services in Thailand
Conclusion
Thailand’s path to becoming a smart manufacturing powerhouse depends heavily on adopting technologies that enable visibility, automation, and resilience. AI manufacturing companies are central to this journey, equipping factories with the intelligence needed to thrive in an Industry 4.0 environment. From international giants like Siemens and ABB to regional innovators like SmartOSC, the companies featured in this blog are helping manufacturers across Thailand transform digitally, remain competitive, and build future-proof operations.
Contact us to explore how we can support your AI-driven manufacturing transformation in Thailand.